The evolution of Surgital packaging
26 November 2024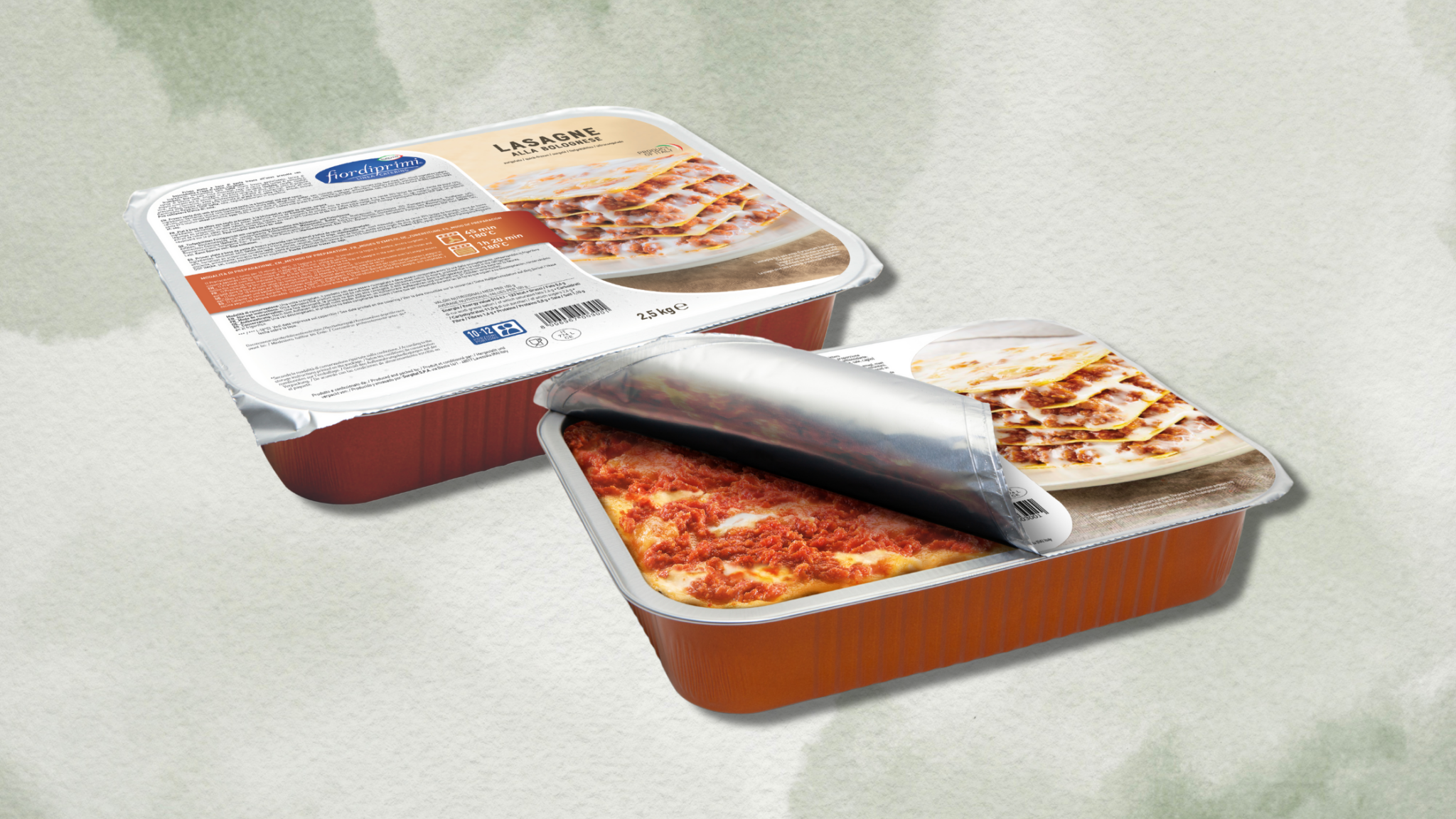
“Reduce, reuse, recycle” is the “3R” motto that guides production and consumption in a circular economy that prioritises environmental sustainability.
These principles are, of course, central in the packaging industry, too: every step, from the design stage onwards, must consider environmental impact, focusing in particular on the choice of materials.
“Minimise” is the watchword, shifting from the take-make-waste logic typical of a linear economy to a model of production and consumption that extends the life cycle of products, thereby reducing waste.
From multi-material to mono-material
We asked Elisa Martini, Technical Packaging Specialist, to explain one of our key advancements: the shift from multi-materials to mono-materials.
We are gradually replacing multi-materials with mono-materials and, where possible, reducing thickness without compromising our high standards of product quality and safety. This change enables us to improve the environmental impact of our packaging.
This undertaking has been a technical challenge for production, representing a significant step forward in sustainable development, also from a logistical point of view.
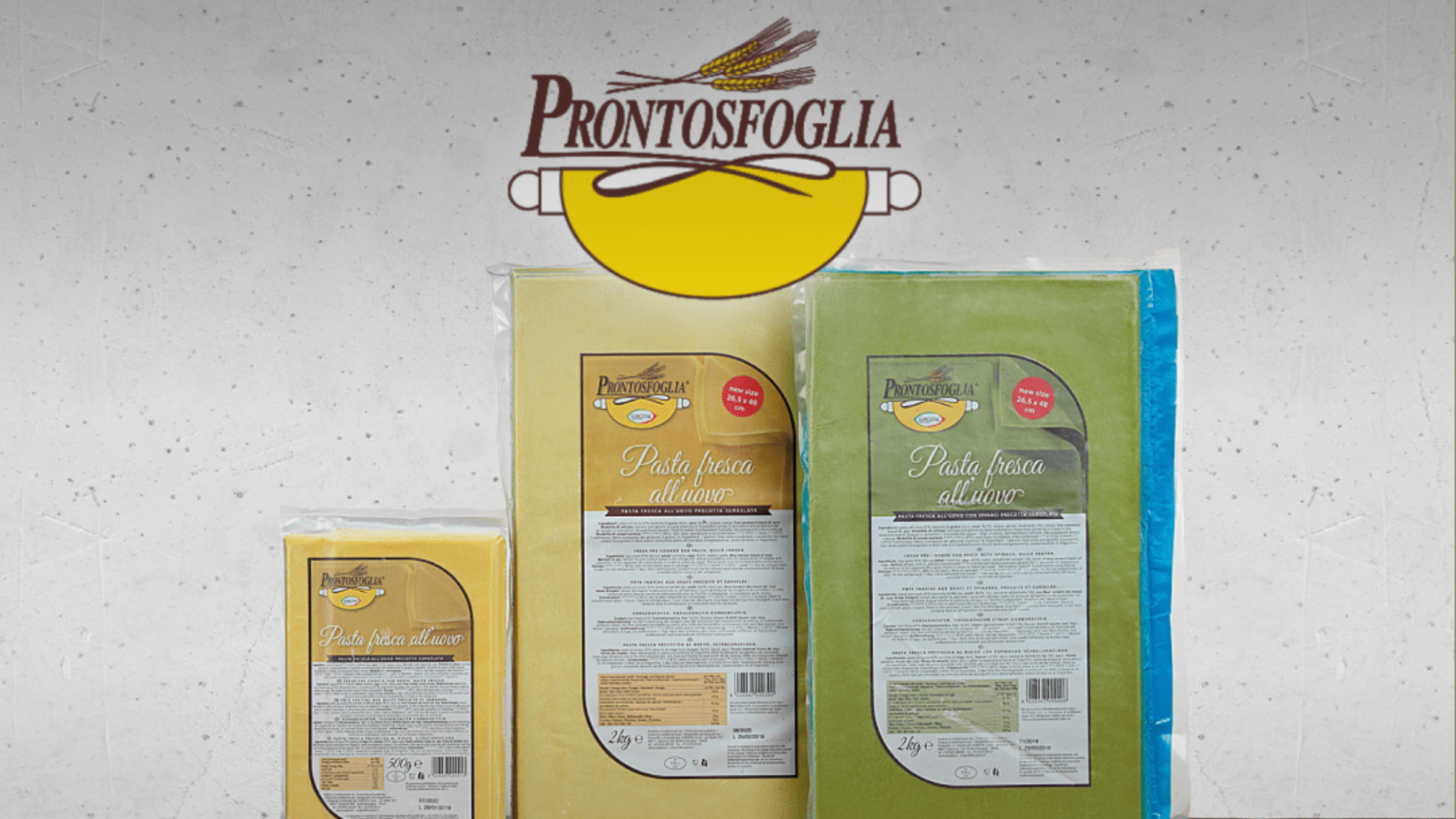
Partnership and innovation for a sustainable future
Our commitment focuses on multi-portion trays. In this case, collaboration with our supplier partners was essential.
“We worked closely with our packaging suppliers and the project involved three key steps,” explains Elisa:
- Researching high-performance materials for a perfect seal;
- Conducting field tests and verifying the results;
- Validating the process through a dedicated protocol to ensure the multi-portion trays were perfectly sealed.
The results met our expectations, confirming that we could eliminate the flow pack while maintaining the highest standards of product hygiene and safety.
The entire project will enable us to significantly reduce plastic and aluminium consumption, achieving an estimated saving of around 9 tonnes of plastic and 4 tonnes of aluminium per year.
The project is currently in its start-up phase and is scheduled for completion by 2024.
This achievement was made possible thanks to the collaboration between our specialised in-house engineers, the skilled workforce across the involved departments, and our external partners, who contributed their expertise to help us reach this important goal.”
Innovation across the board: the Prontosfoglia® and Divine Creations® case study
Our commitment to efficiency is also reflected in our production lines. The Prontosfoglia® range, for example, which is one of the most recognised and widely used, is undergoing an automation process that will reduce plastic consumption by making the packaging thinner and more effective.
“As early as 2019, we reduced the thickness of the plastic bag from 100 to 80 microns, but now we aim to reduce it even more, to further minimise our environmental impact.”
Our high-end Divine Creazioni® range has also been updated.
In the same year, back in 2019, we transitioned to a recyclable mono-material for this range.
The journey towards more sustainable packaging was a complex challenge, but the results we have achieved thus far confirm that we are on the right track.
“Sustainability is a journey that requires continuous innovation and the constant search for better solutions,” Elisa emphasised. “We want to develop solutions that not only reduce our environmental impact but can also be effectively and efficiently incorporated into our production processes. For us, combining innovation and practicality is key, striving for tangible improvements that benefit both the environment and business efficiency.”