Surgital, global pioneers of industrial deep-freezing
30 July 2024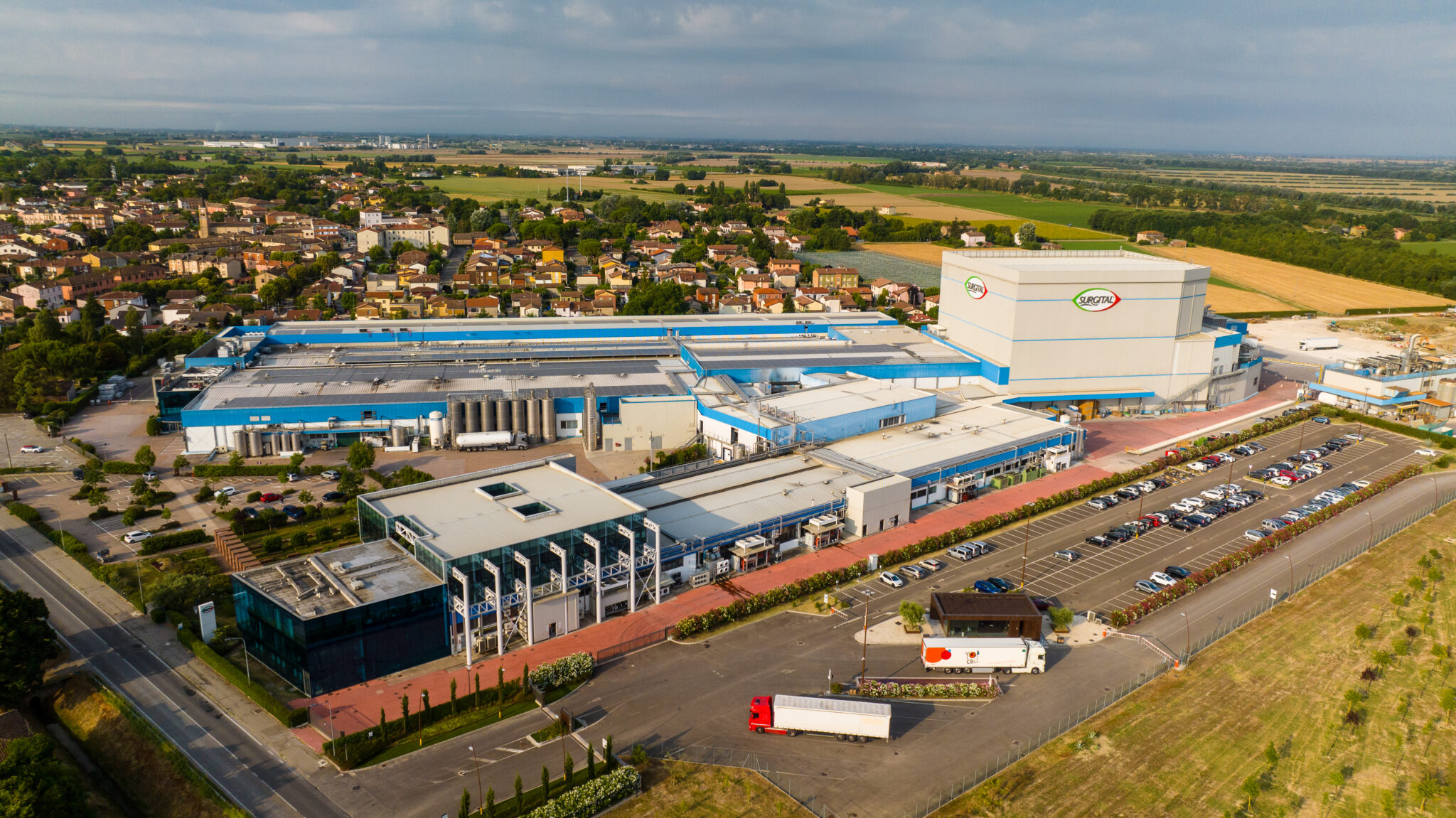
In the current discussion about Italian energy-intensive enterprises, the Emilia Romagna-based group sets itself apart in terms on sustainable innovation.
The company is the Italian and European leader in the use of carbon dioxide in the deep-freezing process.
The industrial plan (2023-2025) includes 20 million EUR earmarked for achieving sustainability goals.
Every day, Surgital produces 160 tons of fresh pasta, 80,000 single-portion ready meals and 12 tons of sauces in pellets, distributed in 60 countries around the world, employing over 350 staff in the Lavezzola facility (Ravenna) and 500 at group level, for a turnover of more than 120 million euros. The leading Italian company in the frozen sector, that understands how valuable freezing is in preserving the quality of food, and for the last 24 years has consequently embraced a philosophy of ongoing experimentation and innovation, constantly reinforcing its commitment to technological progression and the activation of the local economy. In Lavezzola, where all production takes place, the production processes are constantly evolving, adopting the very latest technological innovations in the deep-freezing world, so that the product that is produced preserves all its original qualities and authenticity. Yet beneath the apparent simplicity of the process lies the story of a unique business model.
“We had proved that fresh pasta could be frozen and the demand from the catering industry was unequivocal: we had to evolve into an industrial reality”, says Edoardo Bacchini, CEO and founder of Surgital along with Romana Tamburini. “It was the year 2000 and we discussed it every day with Biguzzi, our engineer. What gas should we use? For a facility like this one, the answer could only be ammonia. But the mayor of Conselice had already rejected its use due to a previous gas leak from another large company. The only alternative was freon which, however, was subjected to large-scale restrictions linked to the ozone hole and the greenhouse effect. But how was it possible, that in the year 2000, there was no other way to produce cold? – I asked myself. That’s how we started, with a pioneering spirit and vision, as well as the belief that we could achieve something great.”
This pioneering spirit was demonstrated by the decision – the first in Italy and Europe – to use carbon dioxide as a refrigerant, an innovative choice that overcame the restrictions linked to the use of ammonia and the environmental limitations of freon. This solution, inspired by a facility in England, was successfully developed thanks to the collaboration with expert technicians, culminating in the creation of an industrial refrigeration system that reached a capacity of 1200 kW and temperatures up to -40°C, exceeding all expectations. By employing IQF (Individual Quick Frozen) technology, the pasta could be rapidly deep-frozen, employing custom parameters and methods for each product type.
Asked what Surgital’s next bold step will be, Edoardo Bacchini replies, “I have always put my faith in scientific research, in experimentation, which is why we earmark our investments every year for finding solutions. Technological solutions that propel us into the future, not just in terms of growth, margins and market share, but also prosperity.
We are a highly energy-intensive company, due to the deep-freezing process requirements. We have, however, always believed in a circular economy where energy can be strategically reused to not only reduce our carbon footprint, but for the benefit of the people who work with us and live in our community. Thanks to the trust placed in our technicians and engineers – who often backed my visions – we have come this far, so now we are ready for the next step.”
Sustainability has, therefore, emerged as a key pillar in the framework of our current industrial plan (2023-2025): 20 million euros were earmarked for the modernisation of systems and facilities at the Lavezzola plant, with the goal of boosting the production capability in an environmentally sustainable way. A new power unit for the cogeneration plant, with an output of 4.6 MW/hour, was also recently installed. The introduction of machine learning software will then optimise the management and calibration of all the energy and thermal drivers, further contributing to the sustainability of the entire production process.
At the same time, the company has recently completed the installation of a new photovoltaic system within the company grounds which will reach a maximum power production of 2.4MW/hour. The company’s ambitious goal is energy self-sufficiency, highlighting how the application of innovative technologies can significantly contribute to the achievement of its goals in terms of sustainability and improved operational performance.